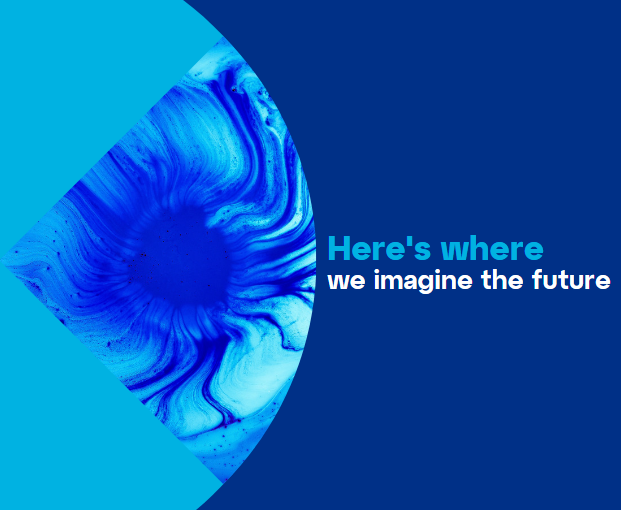
Updates to Annex 1 presents significant practical hurdles for compliance. Here’s where we review the hurdles and highlights 18 months after it came into effect. Deerns has helped the pharmaceutical industry to navigate these higher safety standards with innovative, sustainable solutions.
The updated Annex 1 regulations, came into effect on 25 August 2023,, have set a new standard for the manufacturing of sterile medicinal products in the European Union. The new guidelines address modern challenges such as contamination control, process validation, and technological advancements in manufacturing.
As we reflect on the past year, it’s clear that while the intention behind Annex 1 is to enhance safety and efficiency, its implementation has introduced a range of complexities for manufacturers.
Modernising Manufacturing Standards
Annex 1 is a critical component of EU Good Manufacturing Practices (GMP) that ensures the safety and efficacy of sterile pharmaceutical products. Its revision in August 2022 focused on:
- Strengthening contamination control strategies.
- Emphasising thorough process validation.
- Incorporating modern technologies to improve facility design and operation.
These updates reflect the evolving needs of the pharmaceutical industry but have presented significant practical hurdles for compliance.
Three Challenges Arising from Annex 1 Implementation
Knowledge Gaps and Ambiguity in Regulations: One of the most significant challenges for manufacturers is navigating the technical ambiguity within Annex 1.
" While the regulations set clear goals, their practical application often leaves room for interpretation.
For example, a client producing vaccines for poultry faced difficulties reconciling Annex 1 requirements with overlapping biocontainment regulations.
" Annex 1 prioritised protecting the product from contamination, while the biocontainment standards required safeguarding the environment from the product.
This created conflicting design mandates, requiring innovative solutions to achieve compliance.
Time Constraints: Compliance with Annex 1 often involves retrofitting existing facilities or constructing new ones, which can result in significant downtime. Larger manufacturers are better positioned to absorb the financial impact of phased refurbishments or parallel new builds. However, smaller manufacturers, particularly those with a single production line, face a greater challenge as stopping production for upgrades can lead to substantial revenue loss.
Financial Pressures: The financial burden of compliance is considerable, especially for smaller companies. Upgrading facilities, validating processes, and aligning operations with Annex 1 demand substantial investment. For many manufacturers, balancing compliance with cost-efficiency is a critical hurdle.
Deerns’ Approach to Addressing Challenges
At Deerns, our mission is to provide tailored solutions that address these challenges, ensuring our clients can achieve compliance without compromising their operational or financial goals.
- Client-Centric Analysis and Planning: Deerns collaborates closely with clients to conduct deep operational analyses. We take time to establish long-term relationships so that we can really understand how to bring our clients the best value for money. This involves identifying high-value production areas and prioritising upgrades in a phased manner to minimise financial impact. For example, in one facility, we recommended focusing on refurbishing lower-priority areas first, allowing the client to continue with production while progressively upgrading to meet Annex 1 standards.
- Innovative Design Solutions: Our experience in designing diverse facilities equips us with the ability to resolve complex regulatory conflicts. For the afore-mentioned poultry vaccine facility, Deerns developed a dual-barrier system to ensure product protection while safeguarding the environment. To meet both Annex 1 and biocontainment requirements, we specified cabinets for internal product protection and created innovative pressure cascade systems to maintain product integrity and environmental safety.
- Leveraging Technical Expertise: Deerns’ exposure to facilities across Europe enables us to transfer knowledge between regions. While American FDA, designers and end-users prefer fresh air systems, European entities as EMA, designers or manufacturers prioritise energy-efficient recirculation systems. This deep technical expertise of different design traditions allows us to propose optimal solutions that align with regulatory and sustainability goals.
Sustainability as a Core Principle
Deerns integrates sustainability into its designs wherever possible, even in the face of strict safety and biocontainment regulations. For conventional facilities, we incorporate WELL and BREEAM principles, focusing on energy efficiency, thermal optimisation, and sustainable material use.
" In more complex environments, such as biocontainment facilities, certification may not always be feasible, but the principles of sustainability remain central to our approach.
For example, in a high-containment quality control laboratory, we would typically embed sustainability measures such as efficient HVAC systems and energy optimisation strategies. While certification might not be achievable, our designs uphold the core principles of sustainable development.
Partners in Progress
" Looking back on the 18 months since Annex 1’s implementation, it is clear that the journey has been challenging but ultimately transformative.
The revised guidelines have compelled the industry to adopt higher standards of safety and efficiency.
At Deerns, we take pride in our ability to help clients navigate this complex landscape, combining technical expertise with a commitment to innovation and sustainability. As the pharmaceutical industry continues to evolve, we remain dedicated to leading the way in designing solutions that meet regulatory demands while supporting our clients’ long-term success.